Mallas Wire Mesh Manufacturing Co. supplies stainless steel woven wire mesh in a variety of weave types, including plain, twill, and Dutch weaves. Available in mesh counts from 2 to 500, and wire diameters ranging from 0.02 mm to 2.0 mm, the mesh is suitable for filtration, screening, and structural support. Common materials include stainless steel 304 and 316. This mesh is widely used in industrial processing, architectural detailing, and precision filtration systems due to its strength and corrosion resistance.
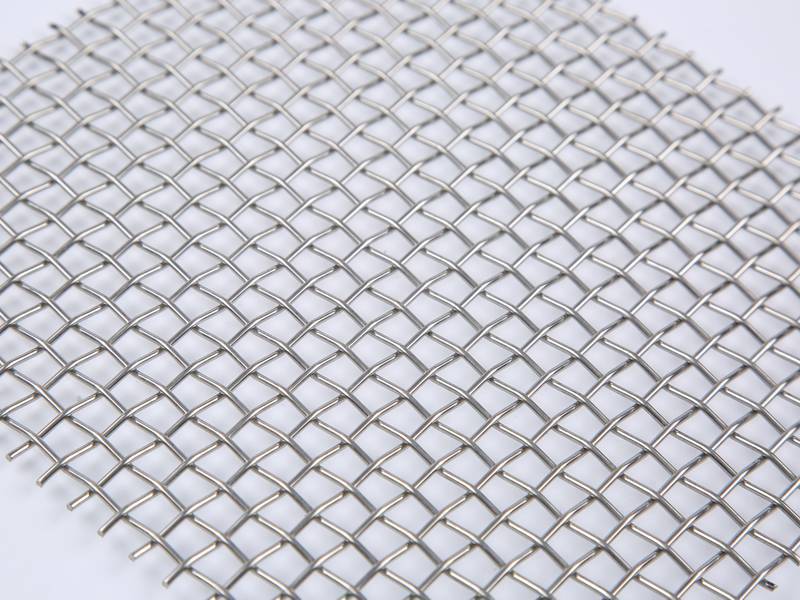
304 stainless steel wire mesh offers good corrosion resistance, strength, and affordability. It’s widely used in general-purpose filtration, screening, and protective barriers for industrial, and architectural applications in non-extreme environments.
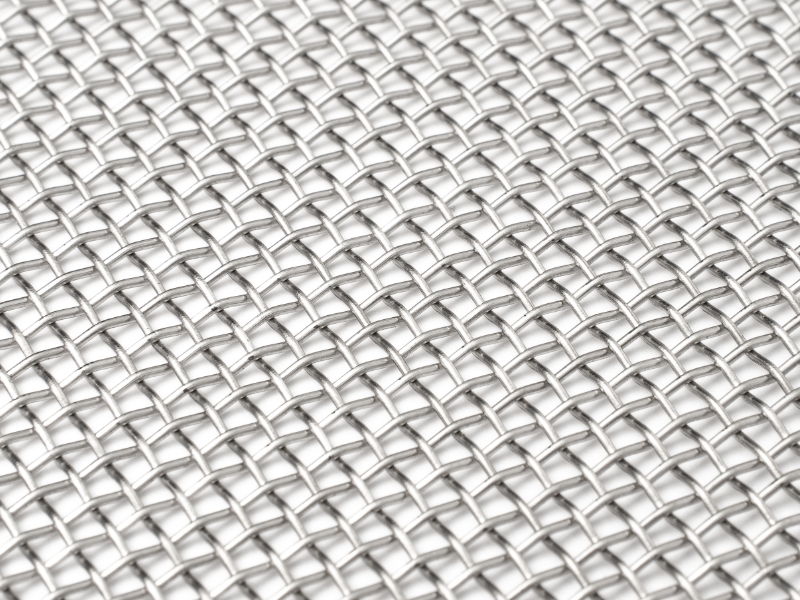
316 stainless steel mesh contains molybdenum, enhancing its corrosion resistance in marine and chemical environments. It is ideal for harsh applications like saltwater filtration, chemical processing, and medical equipment.
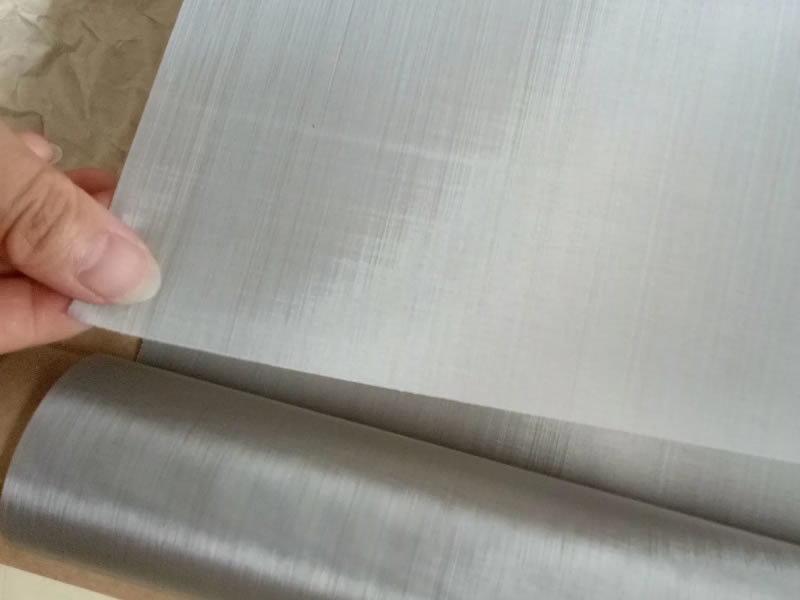
Ultra fine stainless steel mesh features high mesh counts (200–500+), offering precise filtration of very small particles. Common in laboratory, aerospace, and electronics applications where accuracy, consistency, and durability are essential.
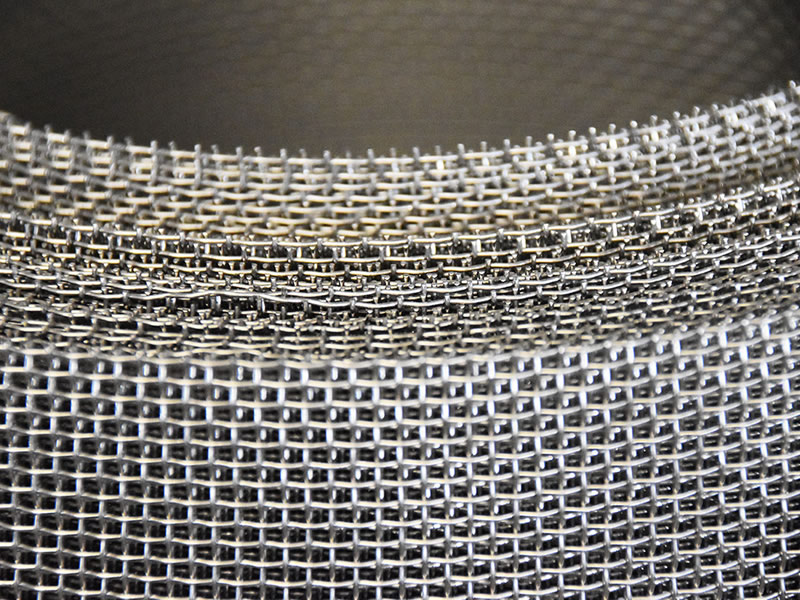
Woven wire mesh screens are versatile, available in various materials and weave types, with mesh sizes tailored to filtration, sieving, and separation applications across industries such as mining, construction, recycling, and agriculture.
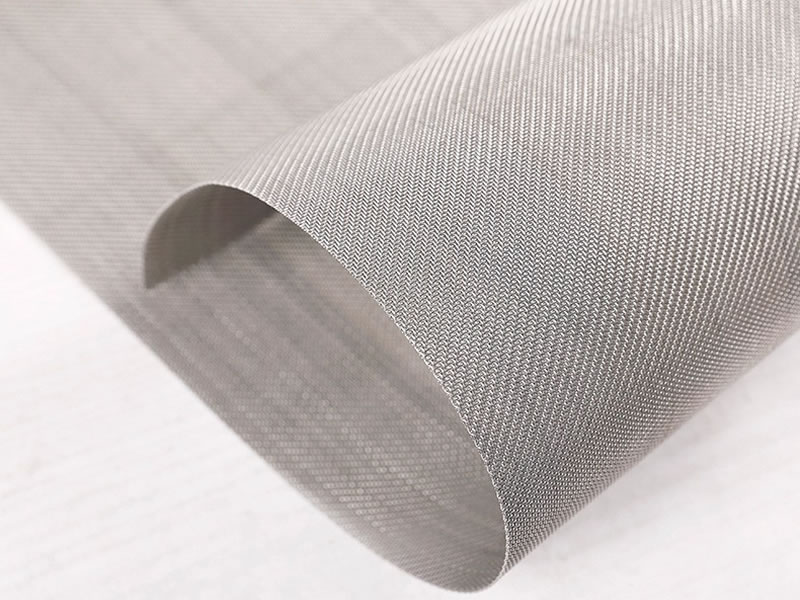
Five-heddle weave wire mesh provides a smooth, flat surface with high mechanical strength and flow-through properties. It’s used in pressure filtration, hydraulic systems, and applications requiring stable, non-marking surfaces.
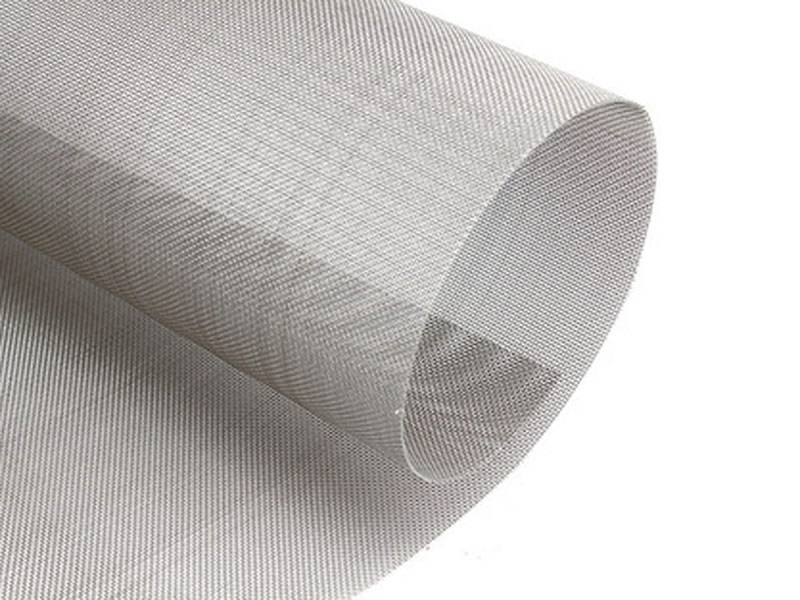
Super Duplex stainless steel wire mesh offers superior strength and exceptional resistance to corrosion, pitting, and stress cracking, making it suitable for offshore, petrochemical, and high-pressure environments where longevity is critical.
Material
- SS 304: Moderate price, general filtration/screening.
- SS 316: Higher price, corrosion resistance for chemicals/marine.
- SS 316L: Higher price, low-carbon variant of 316, superior weldability.
- SS 310: High price, high-temperature resistance.
- SS 321: High price, stabilized for high-temperature service, welding.
- SS 430: Lower price, magnetic, decorative/mild corrosion.
- SS 904L: Very high price, extreme corrosion resistance.
Weaving style
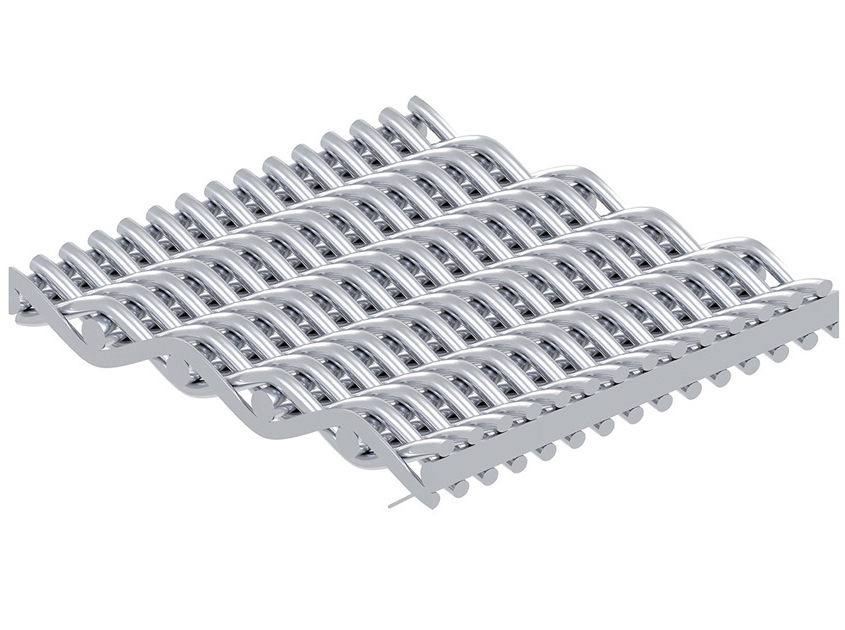
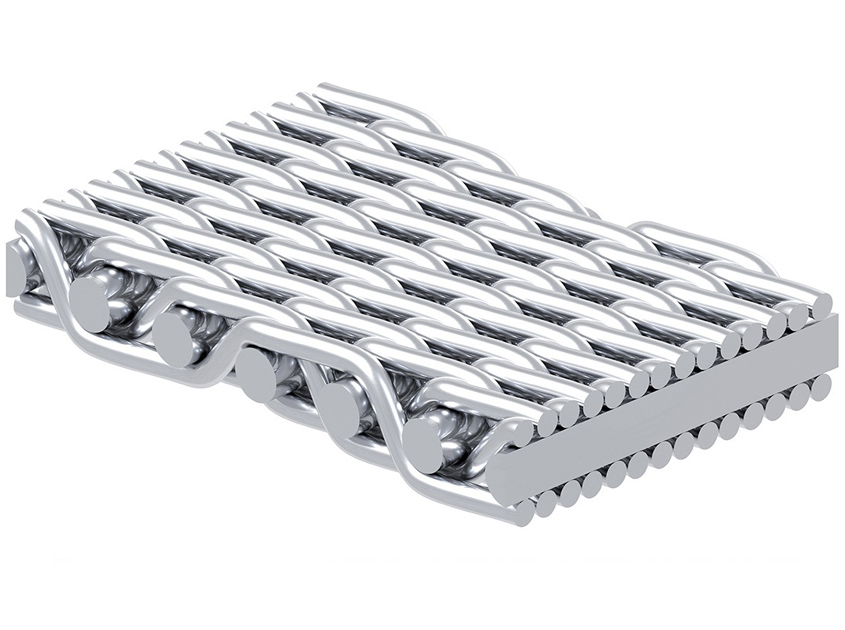
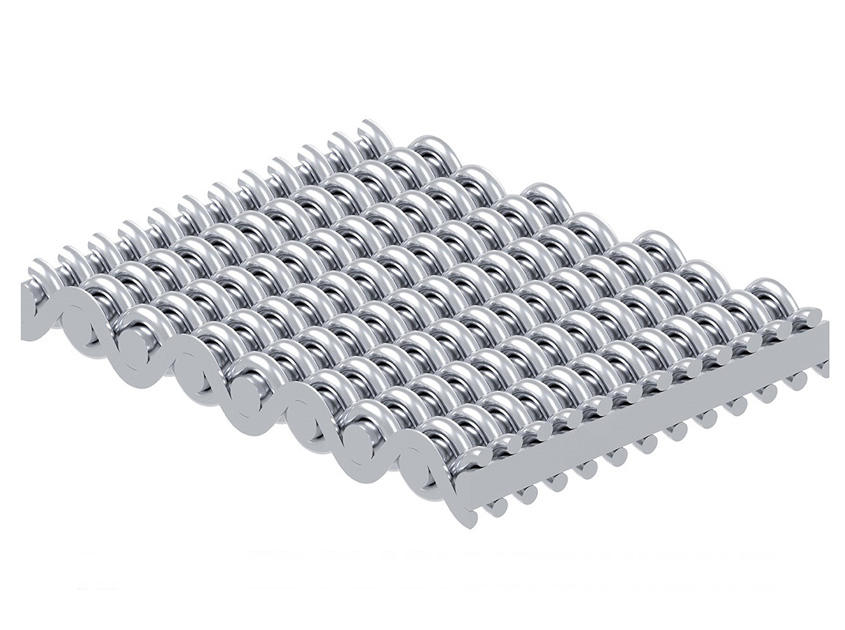
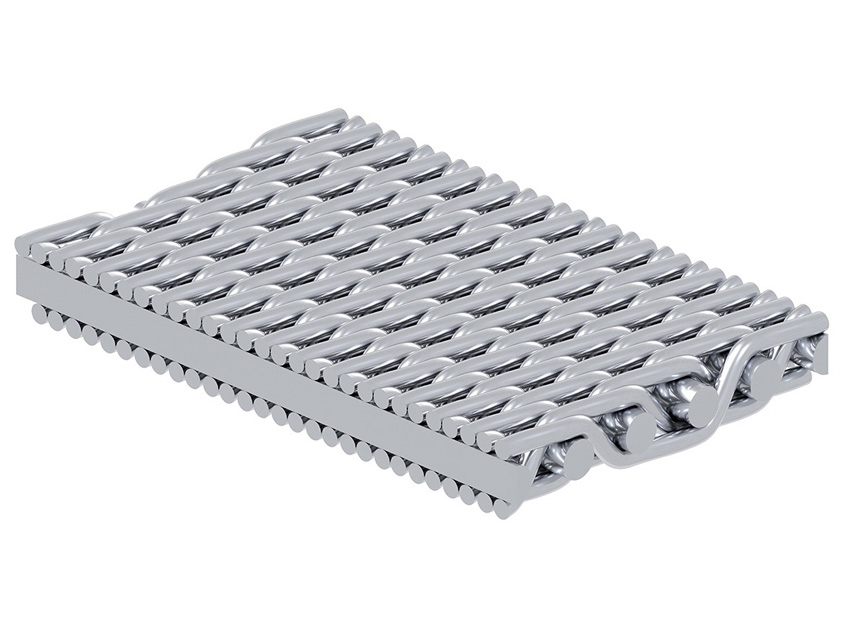
- Plain Weave: The most basic weave where each warp crosses alternately over and under each weft. It provides uniform mesh openings, high stability, and is easy to manufacture. Commonly used in general filtration, screening, and protective barriers.
- Twill Weave: Each warp crosses over two and under two wefts, creating a diagonal pattern. This allows for finer mesh with higher strength and flexibility than plain weave. Ideal for precise filtration in chemical, aerospace, and laboratory applications.
- Dutch Weave: A variation of plain weave with more and finer weft wires than warp. It offers very small openings with a tight structure, excellent for high-pressure liquid and gas filtration, especially in hydraulic systems and fuel filters.
- Reverse Dutch Weave: Opposite of Dutch weave, using thicker weft and finer warp wires. It resists clogging and provides high mechanical strength, suitable for filtering viscous fluids, backflushing systems, and drainage applications.
- Twill Dutch Weave: Combines twill and Dutch styles, with over-two-under-two pattern and dense weft wires. Offers ultra-fine filtration and extreme strength, used in critical industries like aerospace, pharma, and petrochemicals.
- Five Heddle Weave: Warp wire goes over four and under one weft, creating a flat surface with large open areas. It allows better flow and less wear, mainly used in drying, drainage, and paper processing industries.
- Crimped Weave: Wires are pre-crimped to lock tightly at intersections, forming a rigid and strong structure. Best suited for heavy-duty screening, mining, construction, and decorative applications.
General Specifications and Customization
- Mesh Count: Defines openings per inch, ranging from coarse 2 mesh (large particles) to fine 500+ mesh (precise filtration). Common counts: 20, 40, 80, 100, 200.
- Wire Diameter: Impacts strength and opening size. Fine filtration uses 0.025 mm wires; heavy-duty, 2+ mm. Typical: 0.1 mm, 0.5 mm, 1 mm.
- Roll Dimensions: Standard widths: 1, 1.2, 1.5, 2 meters. Lengths: 30-100+ meters. Custom sizes available.
- Aperture/Opening Size: Determines particle passage. Coarse: 25 mm; fine: <25 microns. Common: 0.1 mm, 1 mm, 5 mm.
- Open Area Percentage: Affects flow rate. 20-80+% range. High: increased flow; low: fine filtration.
- Tensile Strength: Resistance to breaking under tension. Vital for high-pressure, vibrating, industrial applications.
- Surface Treatment: Enhances corrosion resistance, durability, cleanliness. Options: passivation, electro-polishing, epoxy, mill finish.
- Temperature Resistance: Withstands heat. Range: 400°C (stainless) to 1000°C (alloys). For furnaces, kilns, exhaust.
- Corrosion Resistance: Depends on alloy/finish. Stainless steel (316, 904L) excels in aggressive conditions.
Aperture Size (mm) | Wire Diameter (mm) | Mesh Size (mesh/inch) | Open Area (%) | Thickness (mm) |
---|---|---|---|---|
1.00 | 0.60 | 18 | 51 | 1.20 |
0.50 | 0.40 | 36 | 48 | 0.80 |
0.25 | 0.30 | 72 | 45 | 0.60 |
0.10 | 0.20 | 150 | 37 | 0.40 |
0.05 | 0.15 | 300 | 30 | 0.30 |
0.02 | 0.10 | 500 | 25 | 0.20 |
This table shows key specifications for woven wire mesh, such as opening size, wire thickness, mesh density, open area, and material thickness